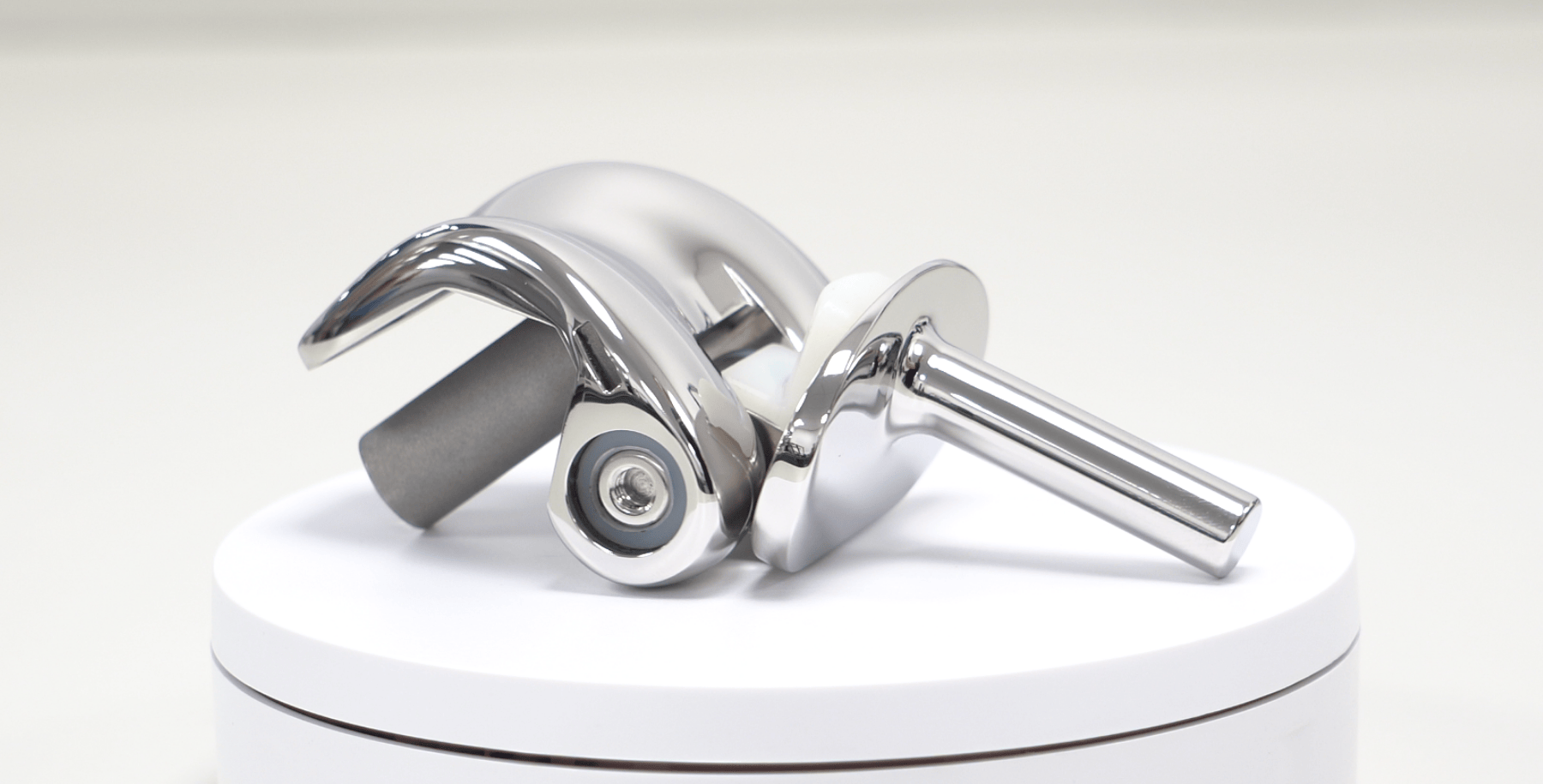
In the dynamic field of orthopaedic implant manufacturing, achieving an optimal polished surface finish on joint replacement implants is critical. A superior surface finish enhances wear resistance, minimises friction, and boosts the long-term performance of the implant. This directly impacts patient outcomes, and the longevity of implants used in knee, hip, shoulder, and other orthopaedic procedures.
At Croom Medical, our expert team carefully selects the most appropriate polishing method based on the type of implant – in terms of design, material, and specific requirements. For complex projects, we often employ a hybrid approach, combining robotic polishing for initial surface preparation with manual polishing for final detailing. An approach that enables us to achieve the precise surface finish required for each unique implant design. In this article, we explore key techniques for joint replacement implant surface polishing, including:
- 1. Drag Finishing
- 2. Hand Polishing
- 3. Robotic Surface Finishing
- 4. Electropolishing
- 5. Chemical Polishing
Join us as we delve into how these techniques contribute to the quality and performance of joint replacements, ultimately enhancing patient outcomes.
1. Drag & Vibratory Finishing
Drag finishing is a mass-finishing technique ideal for polishing large batches of implants such as femoral and glenosphere components. In this process, multiple implants are mechanically “dragged” through a vibratory bowl filled with abrasive media such as ceramic, nutshell, or plastic. At Croom Medical, we use Rossler systems to smooth implant surfaces, removes sharp edges, and ensure a uniform mirror-like finish, enhancing both wear resistance and friction reduction – key factors for joint replacement implant longevity.
Advantages of Drag Finishing:
- Repeatability: Ensures consistent surface roughness across batches, maintaining strict tolerances.
- Batch Processing: Efficiently polishes multiple implants at once, reducing production time and costs.
- Complex Geometries: Particularly useful for polishing intricate, curved surfaces, which are common in orthopaedic implants.
- Enhanced Performance: Improves wear resistance and reduces friction, key factors for joint replacement implant longevity.
- Considerations for Drag Finishing:
- Process sensitivity requires careful selection of abrasive media and process parameters.
- Skilled labour is essential for optimal results.
Best Use Cases of Drag Finishing:
Drag finishing excels in high-volume production environments, especially when manufacturing standard sized implants that require repeatable, high-quality finishes.
Vibratory Finishing
Vibratory finishing complements our drag finishing capabilities, offering another effective method for mass finishing orthopedic implants. The process uses a vibrating bowl or tub filled with abrasive media and the implants to be finished. The vibratory action causes the media and parts to move against each other, resulting in a uniform finish.
Advantages of Vibratory Finishing:
- Versatility: Suitable for a wide range of implant sizes and materials
- Gentle Processing: Less aggressive than drag finishing, making it ideal for more delicate components
- Cost-Effective: Efficient for large batches of smaller implants or components.
Considerations for Vibratory Finishing:
- May require longer processing times compared to drag finishing for achieving the same level of finish.
- Careful media selection is crucial to avoid part-on-part damage.
Best Use Cases of Vibratory Finishing:
Vibratory finishing is particularly effective for smaller implant components, such as bone screws, plates, and dental implants, where a gentler finishing process is preferred.
2. Expert Manual Polishing
For implants that demand precision and customisation, expert manual polishing is unmatched. Experienced technicians use this technique to achieve mirror-like finishes on even the most delicate surfaces and sharp contours. It allows for real-time adjustments, making it an excellent choice for custom implants or highly complex designs.
Advantages of Manual Polishing:
- Unparalleled Precision: Technicians can achieve sub-micron surface roughness levels with exceptional control.
- Flexibility for Custom Implants: Ideal for polishing prototypes and custom designs, allowing for mid-process modifications.
- Optimal Surface Quality: Intricate details such as sharp angles and small contours receive thorough attention, ensuring a flawless finish.
- Real-Time Quality Control: Technicians can immediately identify and address any imperfections, ensuring each implant meets our stringent quality standards.
Considerations for Manual Polishing:
- Time-Intensive: This method is labour-intensive, making it less suitable for high-volume production.
- Skill-Dependent: The quality of the finish is highly dependent on the skill and experience of the technician. We invest heavily in training and retaining skilled polishing experts to maintain consistent quality.
- Potential for Inconsistency: Even slight variations in technique or pressure can result in inconsistencies in the surface finish. We mitigate this risk through rigorous training, standardised procedures, and quality control measures.
Best Use Cases of Manual Polishing:
Hand polishing is best suited for low-volume high mix production, prototypes, or custom implants where precision and attention to detail are essential.
3. Automated Robotic Polishing
Automated Robotic Polishing is an advanced, automated technique that uses an industrial robot arm to ensure consistent and uniform polishing across implants. This method minimises surface defects and variability, making it ideal for large-scale orthopedic joint replacement implant production. While the initial setup is significant, the long-term benefits include increased efficiency, lower labour costs, and improved safety.
Advantages of Robotic Surface Finishing:
- Precision and Consistency: Automation significantly reduces variability and surface defects, resulting in highly durable, wear-resistant implants. This is particularly crucial for our femoral knee systems and hip implants, where surface quality directly impacts longevity.
- Efficiency: Our robotic polishing systems excel at high-speed batch processing, substantially reducing production time. This allows us to meet the growing demand for orthopedic implants without compromising on quality.
- Staff Safety: By automating the polishing process, we’ve eliminated the risks associated with manual polishing machines, enhancing the safety of our team members.
- Repeatability: Robotic systems can replicate the same polishing process with high precision across large batches, ensuring consistent quality across all our implants.
- Data Collection and Analysis: Our robotic systems collect valuable data during the polishing process, contributing to our continuous improvement efforts and R&D initiatives.
Disadvantages of Robotic Surface Finishing:
- Setup and Programming: Requires programming time and setup, especially for custom joint replacement implant designs.
- Limited Customisation: Less flexible for low-volume high mix production or highly customised implants, which may require manual intervention.
Best Use Cases for Robotic Surface Finishing:
Robotic surface finishing is suited for standard joint replacement implant designs in medium to high-volume production environments, where precision, speed, and cost-effectiveness are crucial.
4. Electropolishing
Electropolishing is an electrochemical process used to create ultra-smooth, corrosion-resistant surfaces essential for implant longevity and biocompatibility. The implant is immersed in an electrolyte bath, where controlled electrical currents dissolve microscopic surface layers. This removes irregularities, burrs, and imperfections, resulting in a mirror-like finish that enhances wear resistance and appearance. Electropolishing also passivates the surface, boosting corrosion resistance, minimising contamination, and improving biocompatibility, which is critical for implants exposed to bodily fluids.
Advantages of Electropolishing:
- Surface Quality: Precisely eliminates surface imperfections, resulting in a highly polished, ultra-smooth finish, minimising friction and wear.
- Corrosion Resistance: Forms a passivated surface layer that significantly improves the implant’s resistance to corrosion, critical for long-term stability in the human body.
- Superior Biocompatibility: Reduces the risk of contamination by creating a clean, sterile surface that is less prone to bacterial adhesion, promoting better integration with surrounding tissues.
Disadvantages of Electropolishing:
- High Processing Costs: The multi-step nature of electropolishing, combined with the need for specialised equipment and chemicals, can increase production costs, particularly for smaller batches or highly customised implants.
Best Use Cases for Electropolishing:
Electropolishing is best suited for metallic orthopedic implants such as femoral stems, acetabular cups, and tibial components, where achieving an ultra-smooth, corrosion-resistant surface is critical for both functional performance and long-term durability inside the body.
5. Chemical Polishing
Chemical polishing, or chemical mechanical polishing (CMP), is a surface-finishing technique in orthopedic implant manufacturing that uses controlled chemical reactions to dissolve material. It’s especially useful for complex geometries and intricate features that are hard to polish mechanically. By exposing the implant to specific chemical solutions, surface material is uniformly dissolved, creating a smooth, reflective, and corrosion-resistant finish. As a non-abrasive process, chemical polishing reduces the risk of damage to delicate or intricate components, making it ideal for fragile designs.
Advantages of Chemical Polishing:
- Superior Surface Quality: Electropolishing precisely eliminates surface imperfections, resulting in a highly polished, ultra-smooth finish. This minimises friction and wear, crucial for the longevity of our joint replacement implants.
- Enhanced Corrosion Resistance: The process forms a passivated surface layer that significantly improves the implant’s resistance to corrosion. This is critical for long-term stability in the human body, particularly for our hip and knee implants that are exposed to bodily fluids.
- Improved Biocompatibility: By creating a clean, sterile surface that is less prone to bacterial adhesion, electropolishing reduces the risk of contamination and promotes better integration with surrounding tissues. This is especially important for our patient-specific implants.
- Uniform Surface Treatment: Unlike mechanical polishing, electropolishing treats all surfaces equally, including hard-to-reach areas and complex geometries. This is particularly beneficial for our shoulder implants and foot & ankle implants with intricate designs.
- Stress Relief: The process can help relieve surface stresses induced during manufacturing, potentially improving the fatigue life of the implant.
Disadvantages of Chemical Polishing:
- Material Sensitivity: Careful control of chemical concentrations and processing conditions is required to avoid over-polishing or damaging the implant surface.
- Environmental and Regulatory Concerns: The use of chemical agents requires strict environmental control and proper waste disposal protocols to mitigate the potential impact on both safety and the environment.
Best Use Cases for Chemical Polishing:
Chemical polishing is particularly suited for implants with intricate geometries, such as porous structures, internal channels, or other complex designs. It is also beneficial for materials where minimal mechanical interference is desired, such as fine-grain metallic alloys or implants that require enhanced corrosion resistance without the risk of mechanical wear.
Conclusion
Selecting the right polishing technique in joint replacement manufacturing is essential for optimising joint replacement implant performance and longevity. At Croom Medical, we use a combination of the implant polishing techniques mentioned above to meet the unique demands of each joint replacement implant type and project size. By leveraging these advanced techniques, we ensure that our implants meet the highest standards of quality, durability, and precision.
Looking for expert guidance on your next joint replacement implant manufacturing project? Whether your project involves large-scale production or custom, high-complexity implants, Croom Medical has the expertise and technology to deliver superior results.
Connect with Croom Medical’s highly experienced joint replacement implant manufacturing team for tailored solutions and industry-leading expertise. Contact us today.