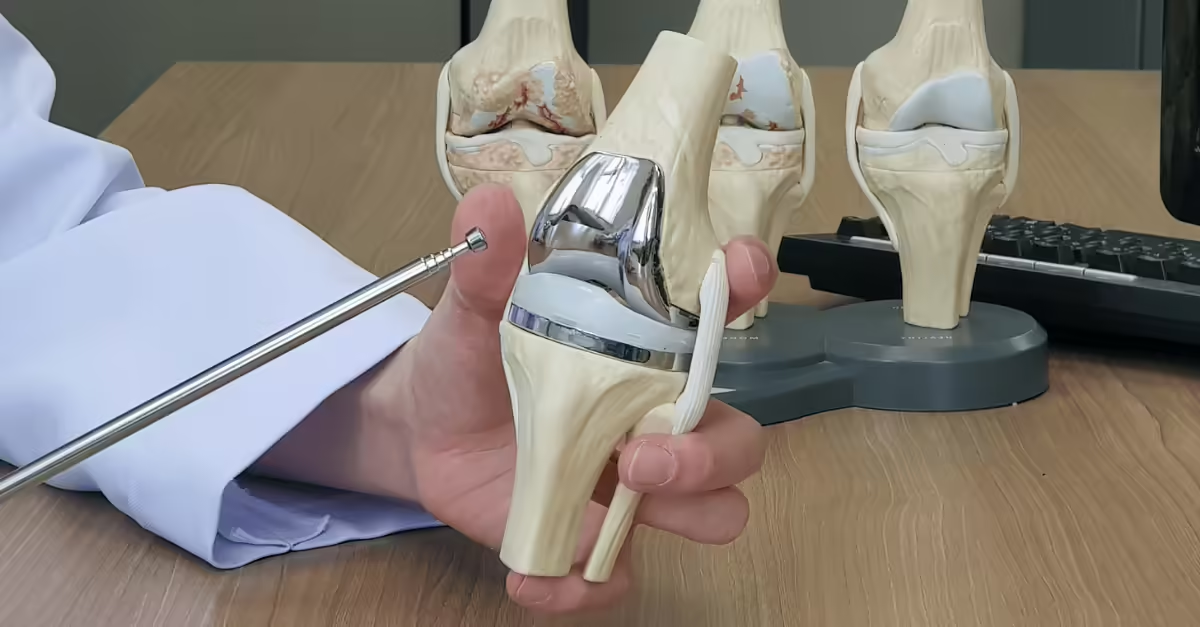
Orthopaedic implant manufacturers face ever-increasing pressure to deliver performance-driven, regulatory-compliant femoral components on time and within budget. But behind each successful implant is a robust, manufacturability-first design approach. That’s where Design for Manufacturability (DFM) plays a critical role.
At Croom Medical, we work closely with OEM partners to optimise femoral component designs for manufacturability from the outset, particularly in complex posterior stabilised (PS) and cruciate retaining (CR) knee systems.
Why Design for Manufacturability Matters in Femoral Component Manufacturing
The knee joint is one of the most mechanically complex in the human body. Every nuance of its design including articulation angles, fixation surfaces, and locking mechanisms has implications for performance, regulatory clearance, and manufacturability.
By applying DFM early in the development process, we help orthopaedic OEMs:
- – Reduce design-to-production timelines
- – Streamline regulatory documentation with clearer tolerancing and geometry control
- – De-risk scaling challenges in both conventional and additive manufacturing
- – Improve consistency in quality and mechanical performance
Moreover, early DFM engagement empowers engineers to eliminate cost-driving features before they become bottlenecks on the manufacturing shop floor.
How DFM Drives Value
Designs optimised for manufacturing yield:
- – Shorter CNC cycle times and lower scrap rates
- – Faster downstream polishing and finishing
- – Seamless integration into automated workflows
Key Insight: A manufacturable design is not just easier to produce. It performs more reliably, scales more affordably, and accelerates time-to-market.
Core DFM Considerations for Femoral Components
Femoral components vary by implant philosophy (PS vs CR), fixation method (cemented vs cementless), and production volume. Yet certain DFM principles apply across the board.
Tolerancing and Geometric Control
Precision is critical in femoral components due to the close articulation with tibial inserts. Tolerancing must account for:
- – Mating surfaces and congruency with polyethylene
- – Radii and chamfers to ease machining transitions
- – Datum structures to facilitate fixturing in multi-axis CNC setups
Our CNC machining platforms, including Hurco 5-axis systems with integrated automation, are specifically tooled to handle complex femoral geometries with micron-level repeatability.
Material Considerations
Most femoral implants use cobalt-chrome or titanium alloys, each presenting different machinability challenges. We assist with alloy selection to balance:
- – Biomechanical performance
- – Corrosion resistance
- – Machining efficiency
Surface Finish Requirements
Posterior stabilised and cruciate retaining designs often require varied surface treatments, including mirror-finished articulation zones and grit-blasted fixation zones. DFM must account for:
- – Accessibility of polishing wheels and media
- – Consistency across batches
- – Preservation of geometry post-polishing
We deploy HAAS Multigrind systems and fully automated polishing cells to ensure precision surface finishes at scale.
Collaboration from Design to Delivery
We believe DFM is most powerful when it’s collaborative. That means engaging with our customers at the concept phase, not after the design is finalised.
Early-Stage Design Reviews
We partner with design teams to assess:
- – CAM toolpath viability
- – Build orientation for additive manufacturing
- – Fixture stability and clamping forces
- – Process stack-ups for surface treatment, laser marking, and cleaning
Our award-winning R&D team provides input grounded in real-world production constraints, ensuring no surprises during scaling.
Bridging DFM and Additive Manufacturing
Where additive manufacturing is used, DFM principles must adapt. We optimise:
- – Build orientation for structural integrity
- – Support structure minimisation
- – Downskin and overhang strategies
- – Post-processing accessibility
At Croom Medical, our additive manufacturing capabilities span platforms from 3D Systems, Renishaw, and GE Concept Laser, enabling flexibility across materials, geometries, and implant designs. Our team ensures AM-based components are fully integrated into the broader manufacturing workflow, from design validation through to finishing and inspection.
Cleaning and Finishing for Regulatory Readiness
Our manufacturing workflows include intermediate cleaning steps that remove all residual particles and machining debris before any component proceeds to inspection or finishing. This enhances regulatory readiness and reduces risk of contamination or delayed validation.
Automation-Driven Scalability
Our investment in automation enables true lights-out manufacturing. Leveraging robotic handling and in-process inspection across our 5-axis machining cells, we deliver:
- – Higher throughput for high-volume PS or CR femoral components
- – Reduced operator error and labour dependency
- – Enhanced consistency for regulatory compliance
This is critical when manufacturing upwards of 175,000 cementless knee components annually for our global OEM partners.
Conclusion
DFM is not just a set of principles, it’s a competitive advantage. By aligning design, engineering, and production teams early in the product lifecycle, orthopaedic OEMs can accelerate innovation and reduce cost without compromising on quality or performance.
At Croom Medical, our expertise in femoral component manufacturing is grounded in collaboration, precision, and a forward-thinking approach to scaling. Whether your implant design is PS, CR, cementless, or cemented, we’re ready to help you optimise it for manufacturability and long-term success.
Looking for expert guidance on your next joint replacement implant manufacturing project? Whether your project involves large-scale production or custom, high-complexity implants, Croom Medical has the expertise and technology to deliver superior results. Connect with Croom Medical’s highly experienced joint replacement implant manufacturing team for tailored solutions and industry-leading expertise. Contact us today.