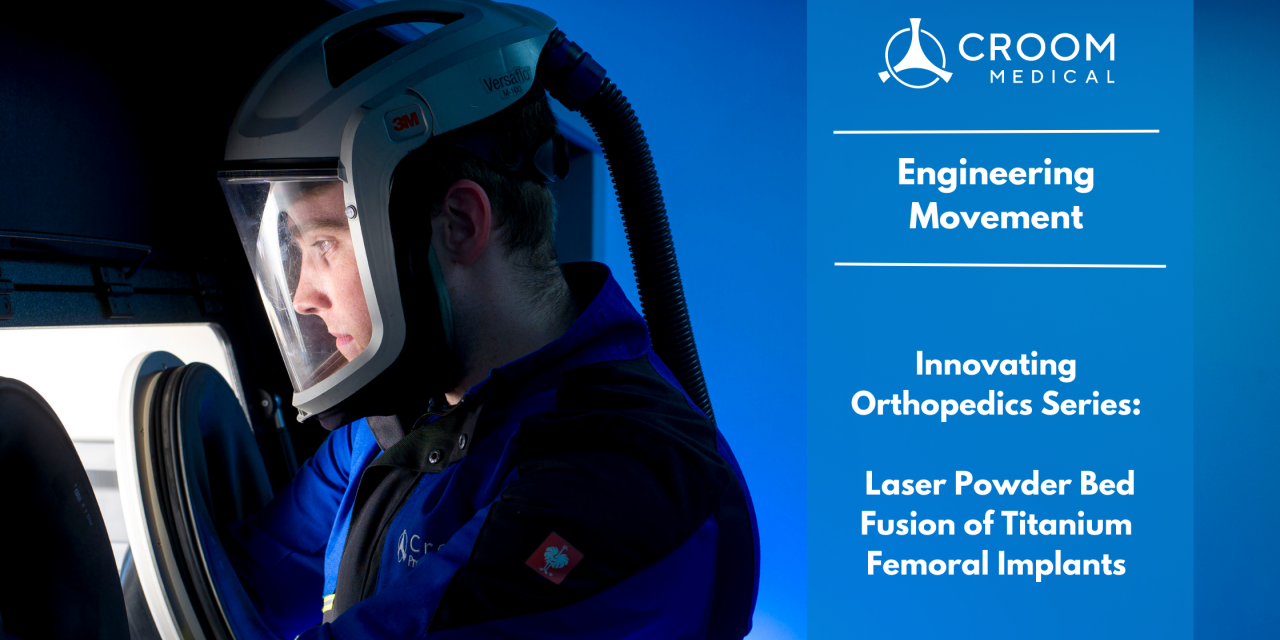
Introduction
Laser Powder Bed Fusion (LPBF) has garnered significant attention as a promising additive manufacturing technique for the production of customized orthopedic implants, such as titanium femoral implants for knee replacement surgeries. Despite the unique capabilities of LPBF, including the creation of complex lattice structures, patient-specific geometries, and the utilization of biocompatible materials, certain challenges, such as cost-effectiveness, quality control, and repeatability, have hindered the widespread adoption of this technology for mass production of femoral implants while ensuring mechanical performance and long-term stability.
This blog will share a snapshot into the mechanical, morphological, and chemistry testing carried out on LPBF-fabricated femoral implants by Croom Medical’s Research, Development, and Innovation (RDI) team, showcasing the potential applications of this technology in the medical device industry.
Section 1: Titanium vs. Cobalt Chrome – Why choose titanium for femoral knee implants?
Cobalt-Chrome has long been the preferred material for various orthopedic product lines. However, recent advancements in manufacturing technology have paved the way for alternative pure and alloyed materials, such as Ti6Al4V, Cp-Ti, and Tantalum (Ta), to emerge as potential contenders. Among these, titanium-based femoral knee implants have gained traction over Cobalt-Chrome (CoCr) implants, owing to their superior biocompatibility, mechanical properties, and manufacturing capabilities. In this article, we will explore the key advantages of employing titanium for femoral knee implants and discuss the factors that contribute to its growing popularity.
- Biocompatibility: Titanium is known for its excellent biocompatibility with human tissue. It has a natural ability to form a stable oxide layer on its surface, which promotes osseointegration and reduces the risk of inflammation and implant rejection. In contrast, Cobalt-Chrome alloys can release metal ions in the body, which may cause allergic reactions or inflammatory responses in some patients.
- Lower Modulus of Elasticity: Titanium alloys have a lower modulus of elasticity compared to Cobalt-Chrome alloys, making them more similar to the mechanical properties of human bone. This similarity reduces stress shielding effects, which can lead to bone resorption and implant loosening over time.
- Lower Density: Titanium has a lower density than Cobalt-Chrome, which results in lighter implants. Lighter implants can reduce stress on the surrounding bone and joint structures, potentially leading to improved patient outcomes and implant longevity.
- Corrosion Resistance: Titanium is highly resistant to corrosion, making it less prone to wear and degradation over time compared to Cobalt-Chrome alloys. This increased resistance contributes to the longevity of the implant.
- Additive Manufacturing Compatibility: Titanium alloys, such as Ti6Al4V, are well-suited for additive manufacturing techniques, like Laser Powder Bed Fusion (LPBF) or Electron Beam Melting (EBM). These technologies allow for the creation of complex, patient-specific geometries and lattice structures, which can enhance implant fit, osseointegration, and load distribution. In comparison, Cobalt-Chrome alloys are more challenging to process using additive manufacturing techniques.
Section 2: Mechanical Testing
Croom Medical hosts an on site materials testing lab in a bid to aid its internal additive manufacturing operations. The following testing criteria are evaluated in order to support these operations:
1.1 Tensile Testing
Croom Medical hosts equipment to assess the ultimate tensile strength, yield strength, and elongation of LPBF-fabricated femoral implants (ASTM E8/E8M)
Our team then Compares the results with those of conventionally manufactured implants and established material standards (e.g., ASTM F75 – (CoCr), ASTM F136 – (Ti6AL4V), ASTM F1537)
1.2 Fatigue Testing
Croom Medical hosts equipment to Evaluate the fatigue resistance of LPBF-fabricated femoral implants under cyclic loading conditions (ISO 7206-4, ISO 7206-6)
Our team then Analyzes the resulting S-N curve and compare it with the performance of conventionally manufactured implants
Section 2: Morphological Testing
Croom Medical leverages its academic partnerships to examine the microstructure of LPBF-fabricated femoral implants using optical and scanning electron microscopy (SEM)
Our team then Investigates the presence of defects (e.g., porosity, lack of fusion) and the effect of post-processing techniques (e.g. Hot Isostatic Pressing, Vacuum Furnace Heat Treatment) on microstructure evolution
2.2 Surface Roughness
Croom Medical hosts equipment to Assess the surface roughness of LPBF-fabricated femoral implants using 3D contact RA testing
Our team then Compares the results with those of conventionally manufactured implants and explore the potential impact of surface roughness on osseointegration and wear resistance
Conclusion
The brief assessment of mechanical, morphological, and chemistry properties of femoral implants fabricated using Laser Powder Bed Fusion (LPBF) offers significant insights into their suitability for orthopedic applications. Croom Medical’s Research, Development, and Innovation (RDI) team has conducted these tests, revealing the potential for LPBF to produce high-quality, patient-specific implants with properties that are comparable, if not superior, to conventionally manufactured alternatives.
As the technology continues to progress, ongoing research and development efforts will be vital to fully harness LPBF’s potential within the medical device industry. Croom Medical collaborates with various industry partners, including Global Advanced Metals, a leading producer of Tantalum material for LPBF systems.
Keep an eye out for our upcoming blog posts on Tantalum material in the following weeks.
About Croom Medical
Founded in 1984, Croom Medical has emerged as a premier orthopedic implant contract manufacturer, focusing on the development and production of groundbreaking medical devices for a multitude of prestigious clients. Situated in Croom, Co. Limerick, Ireland, our organization hosts a team of over 170 which is augmented by an award-winning research, development, and innovation team composed of talented PhD students and post-doctorate staff members who have been fostering core strategic competencies within the company for over a decade.
At Croom Medical, we are committed to investing in advanced technologies, such as additive manufacturing, to deliver state-of-the-art orthopedic solutions. Our highly skilled research, development, and innovation team works closely with clients to design and produce tailor-made implants that cater to specific patient requirements. Upholding a strong dedication to quality, delivery, safety, and ongoing improvement, Croom Medical continues to lead the medical device industry by providing exceptional products that enhance patient outcomes and transform lives.