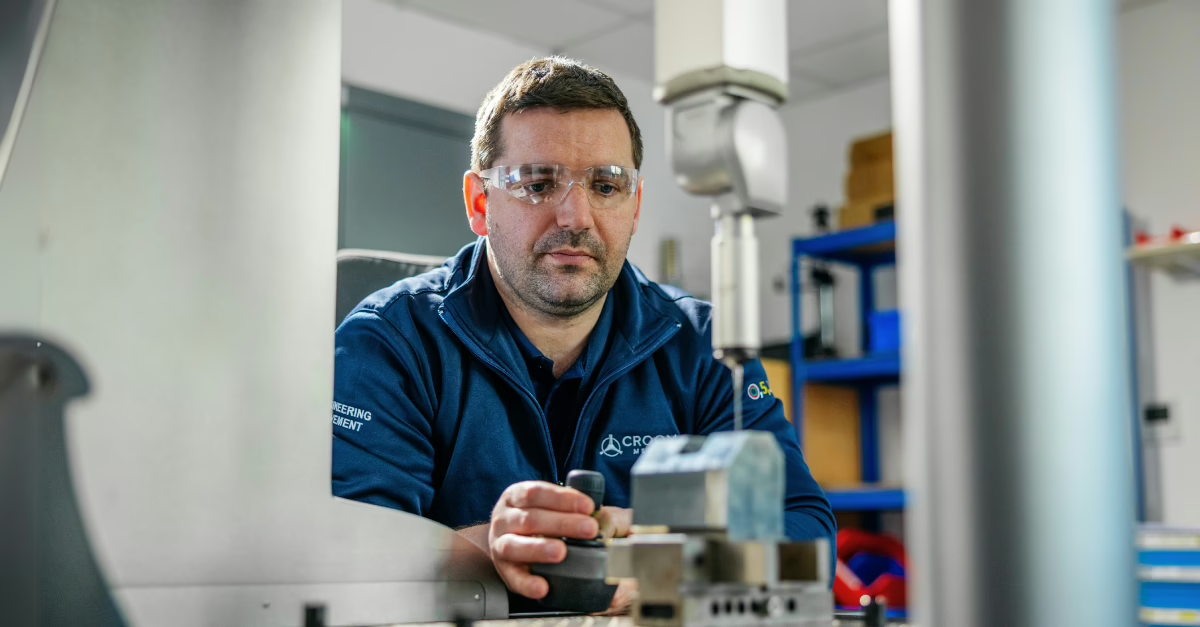
In the world of medical implant manufacturing, the stakes couldn’t be higher. Every implant whether it’s a hip replacement, a cardiac stent, or a spinal screw, has the potential to transform a patient’s life. But with that potential comes immense responsibility. Precision, quality, and safety are non-negotiable, and any misstep can have serious consequences for patient health. That’s why risk management isn’t just a regulatory checkbox, it’s the foundation of everything we do.
At Croom Medical, we understand the critical role risk management plays in delivering safe, effective medical implants. In this blog post, we’ll explore the complexities of risk management in medical implant manufacturing, the regulatory expectations set by the FDA and ISO 13485, and how we integrate these standards into every step of our process to ensure the highest levels of quality and safety.
Navigating the Regulatory Landscape
Medical implant manufacturing operates within a stringent regulatory environment, and for good reason. Two key frameworks guide the industry:
1. FDA Quality System Regulation (QSR)
Under 21 CFR Part 820, the FDA requires manufacturers to establish and maintain a comprehensive quality system that emphasises risk management throughout the product lifecycle. From design and development to post-market surveillance, the FDA’s regulations ensure that every implant is safe, effective, and compliant.
2. ISO 13485
This internationally recognised standard focuses on a risk-based approach to quality management systems (QMS). It covers every stage of the product lifecycle and demands continuous compliance with both regulatory requirements and customer specifications.
Both frameworks share a common goal of safeguarding patient health through rigorous risk management. For manufacturers, aligning with these standards isn’t just about compliance. It’s about building trust with medical device OEMs and patients alike.
Identifying Risk Categories in Medical Implant Manufacturing
Effective risk management begins with identifying the types of risks inherent in medical implant manufacturing. These risks can be broadly categorised into three areas:
1. Design Risks
• Biocompatibility Issues: Implants must be compatible with the human body to avoid inflammation or rejection.
• Mechanical Failures: Fatigue, wear, or fractures can compromise the implant’s functionality.
• Poor Fit: Implants that don’t fit properly can cause discomfort or instability.
• Design Flaws: Overlooked design issues can lead to safety and performance problems.
2. Material Risks
• Incompatibility: Materials that react adversely with the body can lead to complications.
• Corrosion: Over time, corrosion can release harmful particles into surrounding tissue.
• Wear-and-Tear: Debris from material degradation can jeopardise the implant’s integrity.
• Material Defects: Flaws in the material itself can compromise structural integrity.
3. Manufacturing Process Risks
• Contamination: Any contamination during production can lead to infections or other complications.
• Machining Errors: Dimensional inaccuracies can affect the implant’s performance.
• Insufficient Sterilisation: Inadequate sterilisation processes can pose serious health risks.
• Process Variability: Inconsistent manufacturing processes can lead to quality issues.
Strategies for Risk Mitigation
At Croom Medical, we take a proactive approach to risk mitigation, implementing strategies at every stage of development and production.
Here are some of the key approaches we use:
• Design for Reliability: We collaborate with our customers to ensure robust design features and materials to minimise mechanical failures and ensure long-term performance.
• Material Selection: We use proven, biocompatible materials that offer strength, corrosion resistance, and durability.
• Process Validation: Our manufacturing workflows are rigorously validated to reduce variability and ensure consistent results.
• Quality Control: We implement thorough inspections and testing throughout production to identify and rectify defects early.
• Sterilisation Validation: We partner with local & global vendors to ensure sterilisation methods are rigorously tested to eliminate contamination risks.
• Traceability: We maintain end-to-end documentation to ensure accountability and facilitate rapid recalls or investigations if necessary.
Tools to Support Risk Management
To effectively manage risks, industry-standard tools and methodologies can be leveraged:
• DFMEA (Design Failure Mode and Effects Analysis): This tool helps identify potential design vulnerabilities and implement preventive measures before production begins.
• PFMEA (Process Failure Mode and Effects Analysis): PFMEA is used to target and mitigate risks in the manufacturing process, improving reliability and consistency.
• Risk Management Software: Centralised risk management software streamlines risk assessments, monitoring, and documentation, ensuring compliance and efficiency.
Croom Medical’s Commitment to Risk Mitigation
As a trusted manufacturing partner for leading orthopedic OEMs, Croom Medical plays a critical role in the risk management process. Our commitment to mitigating design, material, and manufacturing risks ensures that we deliver safe, high-quality implants that meet the highest industry standards.
Key Contributions:
• Dimensional Accuracy: Using cutting-edge metrology equipment, we ensure precise component fit, preventing assembly issues in final implants. To validate our inspection methods, we conduct Measurement System Analysis (MSA) studies, ensuring the accuracy and reliability of our measurements.
• Surface Finishing Expertise: Our advanced polishing and coating techniques enhance biocompatibility, improve tissue integration, and reduce wear.
• Material Traceability: We maintain comprehensive documentation to track materials from sourcing to production, ensuring accountability at every stage.
• Process Validation: Our robust control systems minimize variability and enhance product consistency.
Unique Capabilities:
• Vertically Integrated Management System: Accredited to ISO 13485:2016 and FDA-registered, we maintain industry-leading compliance standards.
• Advanced Technologies: Investments in 5-axis CNC machining and high-speed manufacturing ensure superior precision and efficiency.
• Experienced Team: Our skilled engineers and technicians bring deep expertise in medical implant manufacturing, ensuring that every product meets the highest quality standards.
Conclusion
Risk management is more than a regulatory requirement. It’s a cornerstone of patient safety and product quality. By adhering to FDA and ISO 13485 standards, manufacturers can deliver medical implants that not only meet regulatory expectations but also drive positive patient outcomes and build trust with healthcare providers.
At Croom Medical, we take pride in our compliance and risk management expertise. With state-of-the-art manufacturing technologies, strict quality controls, and a commitment to continuous improvement, we’re dedicated to enhancing healthcare through safer, more effective implants.
Looking for expert guidance on your next joint replacement implant manufacturing project? Whether your project involves large-scale production or custom, high-complexity implants, Croom Medical has the expertise and technology to deliver superior results.
Connect with Croom Medical’s highly experienced joint replacement implant manufacturing team for tailored solutions and industry-leading expertise. Contact us today.