Home / Insights / Whitepaper /
Observations on the Stability of Tantalum Powder during Laser-Powder-Bed-Fusion Additive Manufacturing
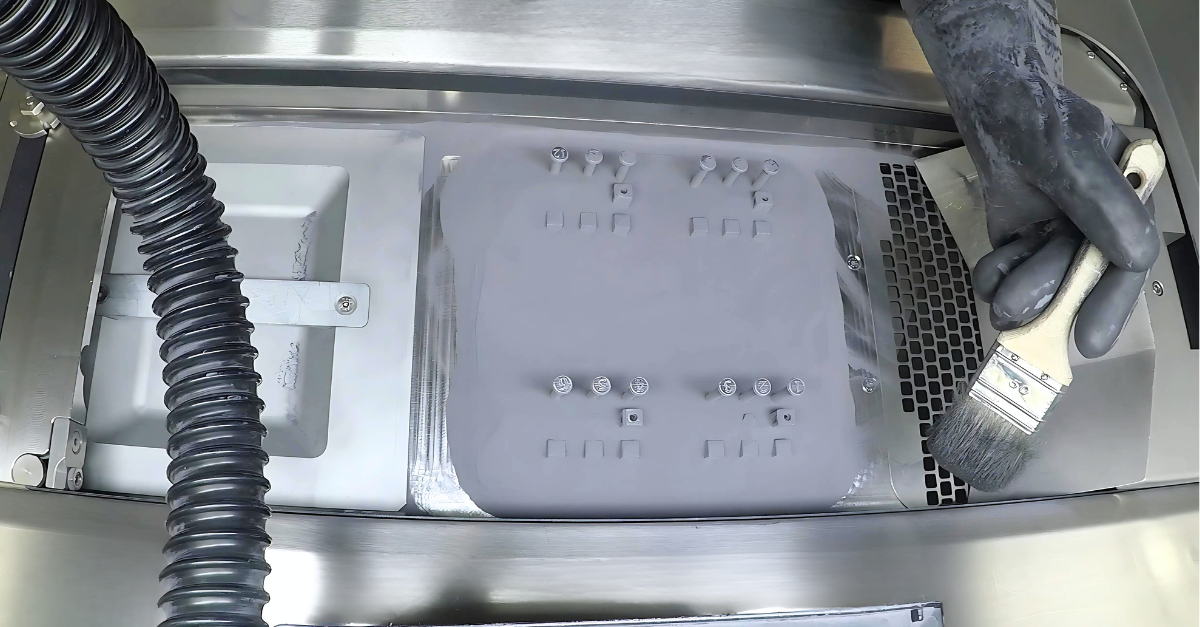
Authors: Dr. Matthew Osborne1, Dr. Gordon Smith1, Dr. Bryan Naab2 , Dr. Shane Keaveney2
Companies:1Global Advanced Metals (Boyertown, PA, USA) & 2Croom Medical (Limerick, Ireland)
Tantalum (Ta) is a rare metal that provides unique, advantageous properties for a variety of industrial sectors including excellent performance at elevated temperature, high corrosion resistance, and high osseointegration promotion for medical implant. The use of Ta is often limited due to a very high melting point (3000oC) and difficulties in fabrication. The use of Additive Manufacturing (AM) / 3D printing can greatly overcome the fabrication difficulties, allowing for the creation of complex structures and near-net-shape manufacturing with reduced machining requirements. The inherent benefits of AM reduce material waste, costs, and lead time, as well as enable higher design freedom.
Within AM, the reusability of feedstock powders strongly influences build costs, and it is therefore advantageous to sieve and reuse the powder as many times as possible. In this paper, the data will show that Global Advanced Metals (GAM) Ta powder can be reused over multiple months and builds. The work was performed using a GE M2 Laser Powder Bed Fusion (L-PBF) 3D printer at Croom Medical (CROOM), Limerick, Ireland.
During laser AM processing, the powder is subjected to intense, rapid heating and cooling cycles which can result in chemical reaction with chamber gases, partial melting of the powder particles, and expulsion of particles from the powder bed. For powders which are recycled, the net effects are an increase in gas content (oxygen, nitrogen, hydrogen), oversized particles in the form of welded agglomerates, and loss of finer particles. In general, oversized particles are removed by sieving of the powder between builds. The loss of finer particles is not detrimental to the powder performance, although it can influence powder flowability and hence powder dosing and the surface roughness of the printed part. The primary concern with the reuse of Ta powder in L-PBF is an increase in gas content, especially oxygen, leading to influence on mechanical performance (see Figure 1).
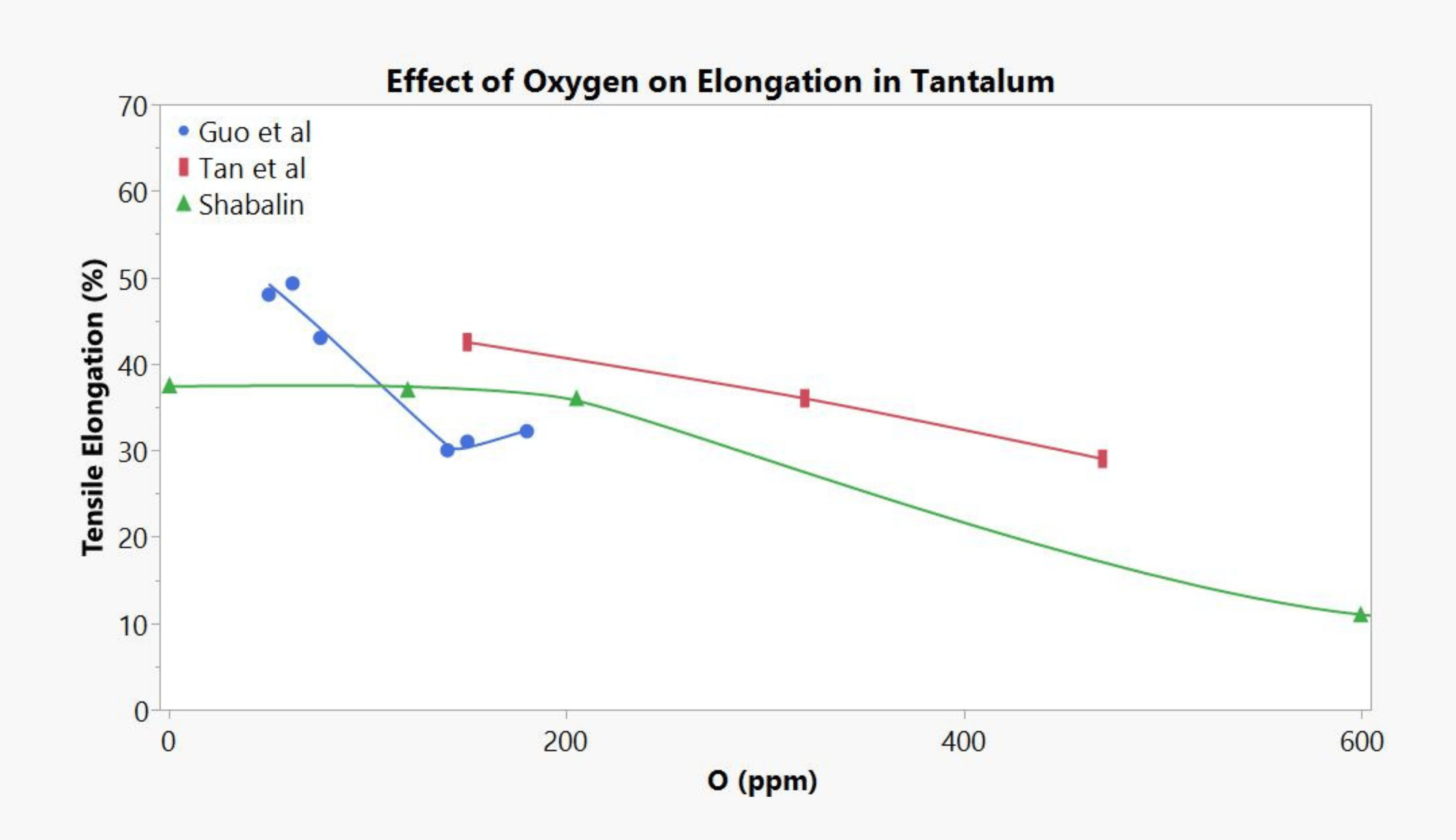
Figure 1. Effect of Oxygen on Elongation in Tantalum. Electron beam powder bed fusion (EB-PBF) data from Guo et al., L-PBF data from Tan et al., and wrought data from Shabalin.
GAM and CROOM are working together to create osteopathic implants of Ta as its yield strength and elastic modulus, when printed in a porous form, closely match that of cancellous bone. Additionally, Ta causes no immune response from the body, and has superior osseointegration compared to Titanium alloys and Cobalt-Chromium (CoCr). Moreover, AM Ta has displayed exceptionally high levels of ductility in the as-built state leading to excellent resistance to fatigue crack propagation. Key properties, such as density and fatigue life, can be negatively affected by excessive oxygen content, so it is desirable to minimize oxygen in the starting powder and control absorption during AM processing.
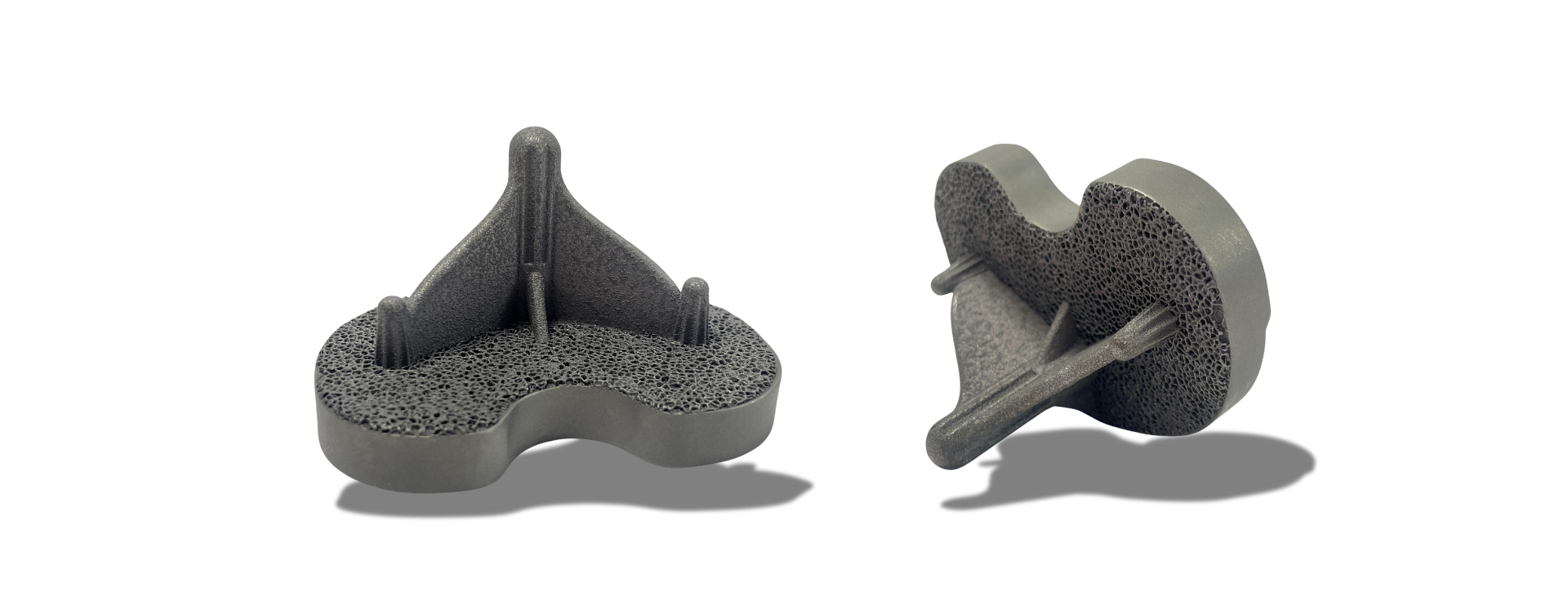
Figure 2. Prototype Titanium-Tantalum Hybrid Implant 3D-printed by Croom Medical.
Croom Medical established the Ta print platform by refining additive process parameters, exploring build strategies, and testing a variety of structures over multiple builds. Two development campaigns using separate lots of Ta feedstock powder were used during the development. Ta powder samples were taken before and/or after select builds to perform a significant number of analytical tests. Oxygen analysis was performed at GAM using LECO inert gas fusion analysers with the powder oxygen data shown below. Note that oxygen monitoring was not part of the experimental design at the time the samples were gathered, so scatter in the data is larger than may be expected with a more controlled experiment.
Campaign A (Figure 3, left) was a series of nine builds using one powder lot. The initial powder oxygen was 155 ppm (dashed line) and the oxygen values for each subsequent build are near the starting value and calculate to a 5% loss in oxygen over the campaign.
Campaign B (Figure 3, right) was a series of 6 builds using a virgin powder lot. This lot also had 155 ppm starting oxygen content and the subsequent data also are near the starting value with an overall increase of about 20 ppm or 3 ppm per build. These results show less oxygen pickup than EB-PBF results reported by Guo et al. who saw a near-linear increase in oxygen from 40 ppm in the virgin powder to180 ppm after 30 times reuse (about 5 ppm per build). For a comparison across materials, Koushik et al. studied the reuse of Ti-6Al-4V powder in L-PBF and found an increase in oxygen from ~1060 ppm to ~1280 ppm (about 22 ppm/build).
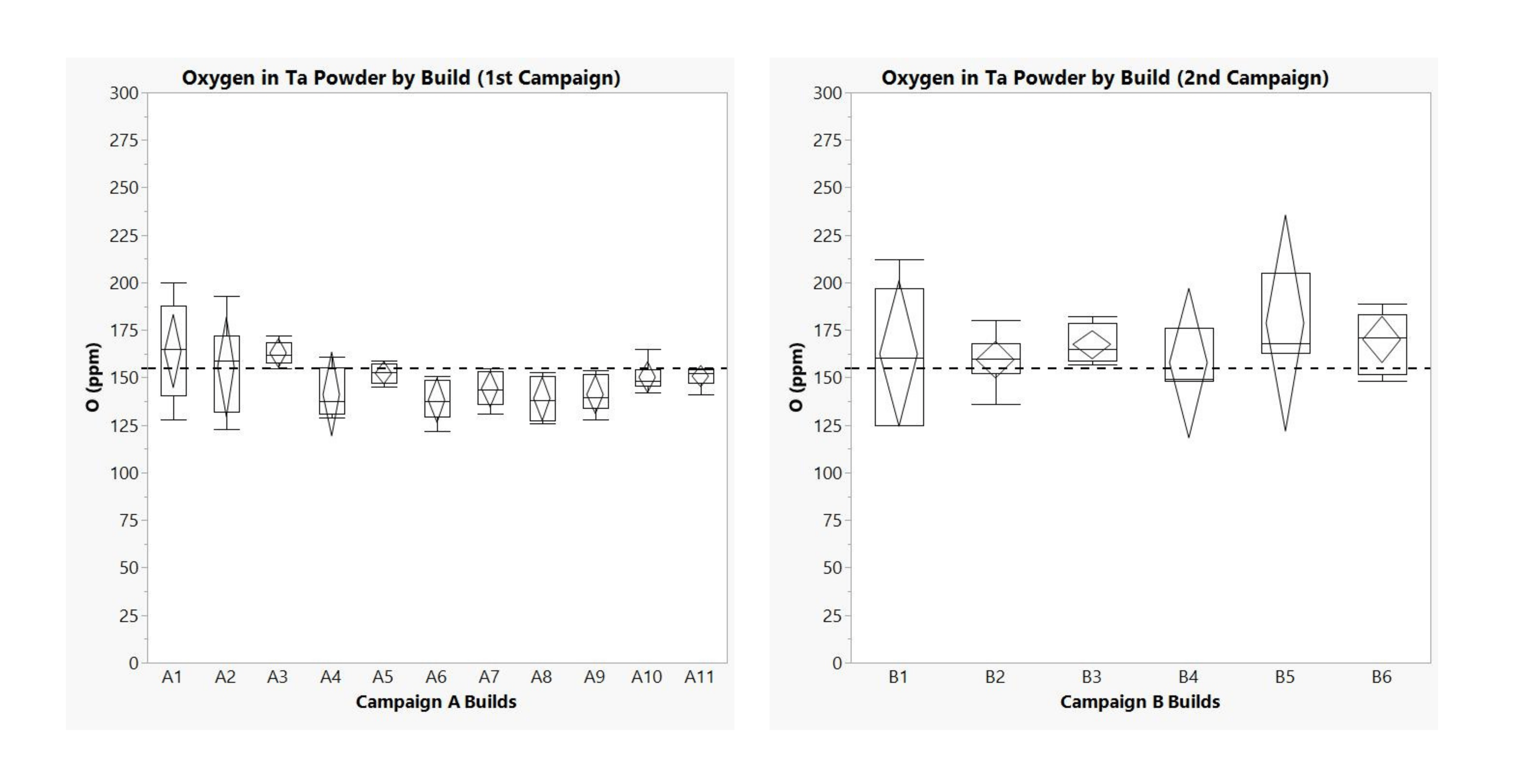
Figure 3. Oxygen in Ta Powder for (left) Campaign A and (right) Campaign B.
Experimental work is in progress to specifically isolate and examine the effect of powder reuse. Results including oxygen values, powder properties, and mechanical properties of the build parts will be reported in near future.
In summary, the analysis of Ta samples printed at CROOM using GAM’s powder shows that the combination of the processing conditions and powder allow for significant powder reuse with little or no increase in oxygen. The designed study currently in process is focused on more closely examining the changes in oxygen and connect any changes with trends in powder and printed material properties.
References
Y. Guo, C. Chen, Q. Wang, and M. Liu, Effects of reuse on the properties of tantalum powders and tantalum parts additively manufactured by electron beam powder bed fusion, Mater. Res. Express, 8, 2021.
C. Tan, Q. Shi, K. Li, K. Khanlar, and X. Liu, Effect of oxygen content of tantalum powders on the characteristics of parts processed by laser powder bed fusion, Int. J. Refract. Met. Hard Mater., 110, 2023.
I. Shabalin, Ultra-High Temperature Materials I, Ch. 6, Springer Science + Business Media Dordrecht, 2014.
T. Koushik, S Shen, W.H. Kan, M. Gao, J. Yi, C. Ma, S.C.V. Lim, L.N.S Chiu, and A.Huang, Effective Ti-6Al-4V powder recycling in LPBF Additive Manufacturing Considering Powder History, Sustainability, 15, 2023.