Home / Insights / Case Study /
Spine OEM Overcomes Additive Manufacturing Challenges with Croom Medical
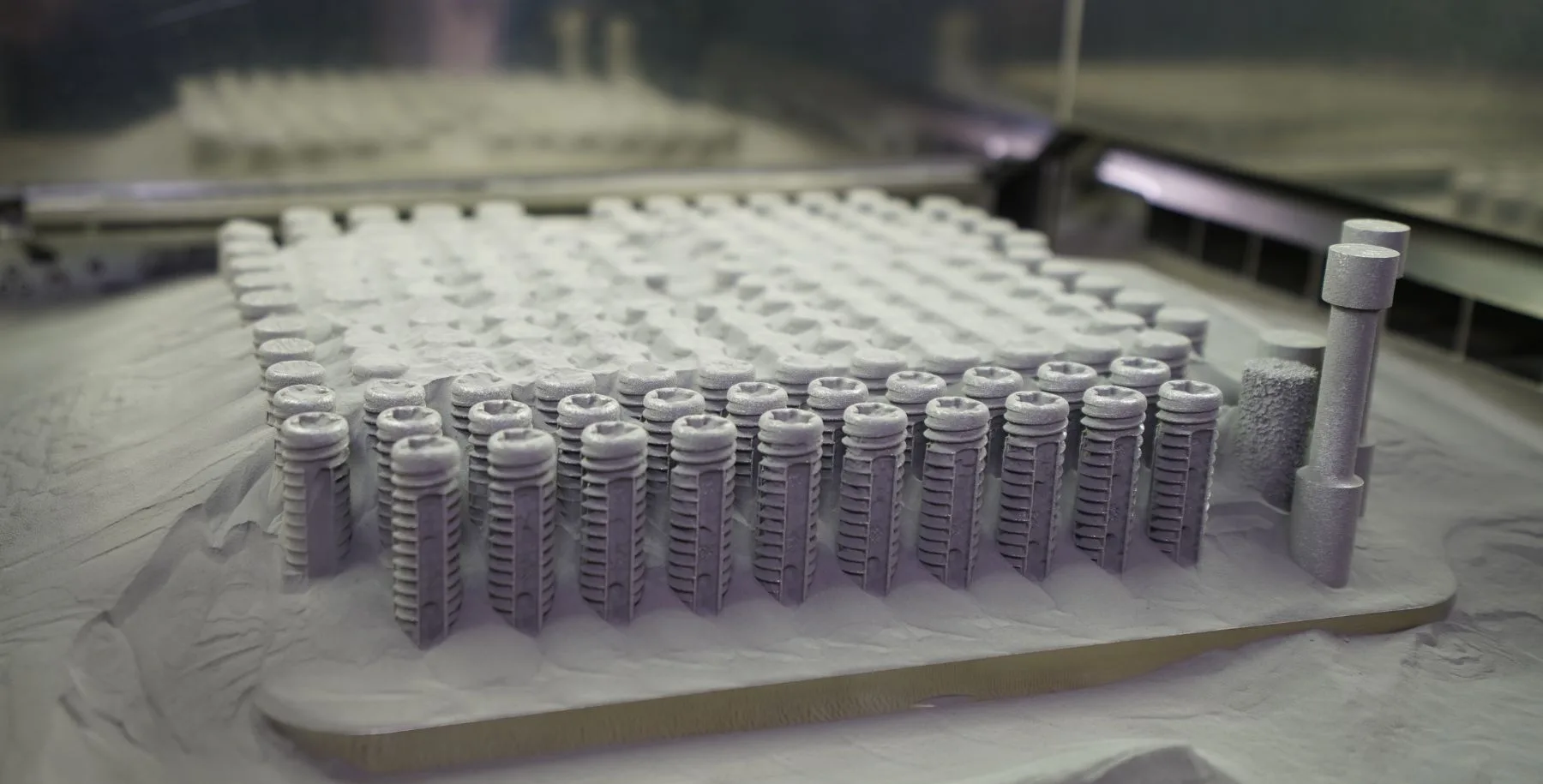
A trusted partner for precision Additive Manufacturing
A pioneering leader in spine implants based in the US, sought a development partner with proficient expertise in Direct Laser Melting Systems (DMLS) to enable precision Additive Manufacturing (AM) of their innovative product for the market, a SI Joint Fixation Screw. With previous vendors falling short, they turned to Croom Medical, trusted for their collaborative approach and deep expertise.
Croom Medical’s Research and Development team is known for its ability to push the boundaries of Additive, enabling the production of medical devices with intricate designs and complex features. The team’s involvement in industrial and academic partnerships for 10+ years coupled with their active participation in Research Consortiums has significantly broadened their understanding of Additive Manufacturing for orthopedic implants and extended their network.
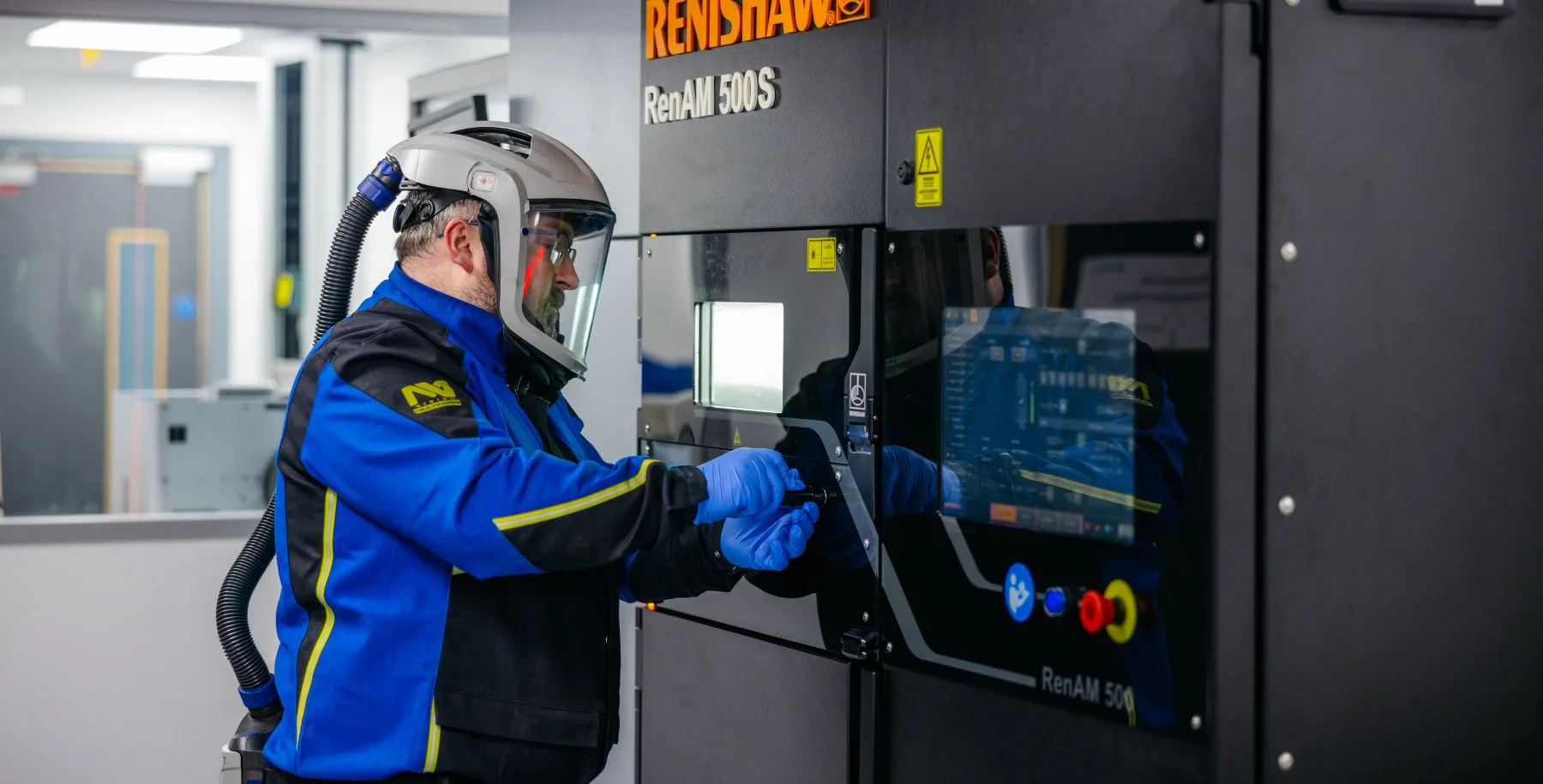
Additive Manufacturing Engineer using Renishaw’s RenAM 500S technology, well-suited for printing Spine Implants that require precision.
Overcoming a series of development challenges
The Spine OEM presented Croom Medical’s team with one of their products, a Sacroiliac Joint Fixation Screw early in its development phase. The screw had a number of intricate features, presenting a significant challenge to 3D Print successfully. Previous attempts by vendors using other printing platforms had failed.
Croom Medical were our 5th vendor to try and make this work. Others vendors AM platforms weren’t good enough to print the features on the product. Nobody else could manufacture our component effectively.
The complexity of the screw’s design, including fine-threaded features, posed difficulties during the printing process due to excessive heat build-up, resulting in warping and deformation of the component. Achieving accurate printing of such intricate features on the screw was going to prove as a difficult task.
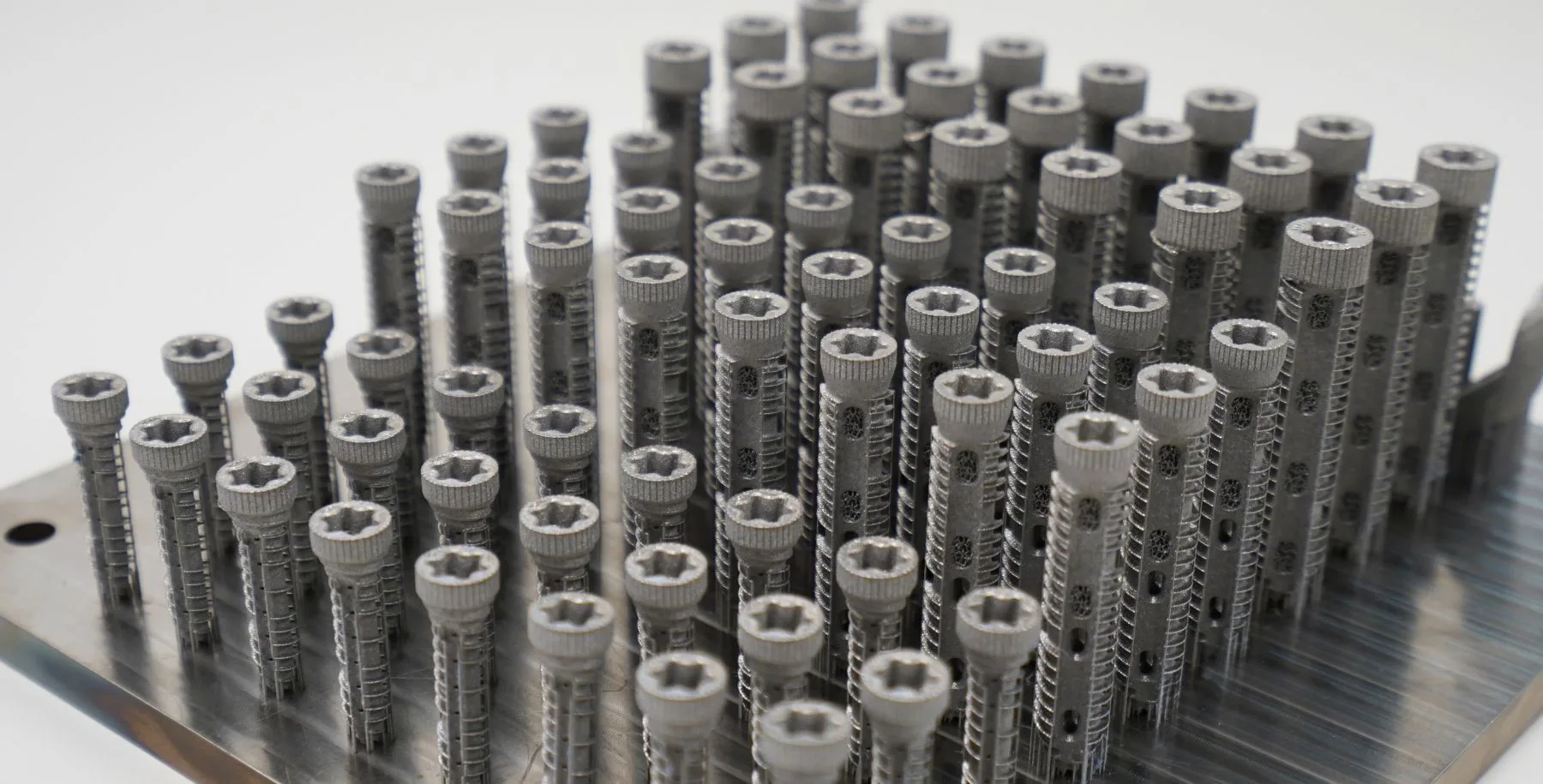
A batch of SI Joint Fixation Screws fresh off the Renishaw printer at Croom Medical’s Additive Technology Lab.
The solution for successful AM production
To support the Spine OEM in overcoming the printing challenges and advancing their product development, Croom Medical leveraged their knowledge in Additive Laser-Powder-Bed-Fusion (LPBF) platforms to develop an approach that would enable the customer to successfully manufacture their product and launch to market.
1. LPBF technology enables print of fine features
Croom Medical used Laser-Powder-Bed-Fusion technology, specifically the Renishaw RenAM 500S, known for its point exposure capability. This advanced technology enabled Croom Medical to successfully print the fine features of the screw while effectively managing heat-related issues.
2. A smart support strategy for precise implant printing & easy post-processing
Croom Medical R&D team developed a support strategy to facilitate the effective printing of the screw while ensuring ease of removal post-printing. The design, style and positioning of the supports was crucial in overcoming challenges such as implant warping and bending during the printing process.
We developed multiple iterations of designs to identify the right way to support the component during printing. They needed to be strong enough to support fine features on the screw, while being easily removable during post-processing.
3. Developing a series of SLM-compatible osteoconductive porous structure
The Spine OEM faced a challenge as their existing lattice structure, designed for Electron Beam Melting (EBM), was not compatible with Selective Laser Melting (SLM) technology.
The Spine OEM didn’t have a porous structure for SLM, as their existing lattice structure was designed for Electron Beam Melting (EBM). To overcome this challenge, Croom Medical’s team replicated the OEM’s existing lattice structure, making necessary adjustments to ensure suitability for SLM. A range of options was presented to the customer to meet their specific needs.
To support the customer in decision making, Croom Medical’s team conducted a series of tests and experiments. These trials assessed the performance of various printing and designs parameters to achieve the desired lattice structure for the OEM. After thorough analysis, the customer selected their preferred lattice structure. From there, Croom Medical applied this chosen lattice structure across the range of product sizes within the Screw family.
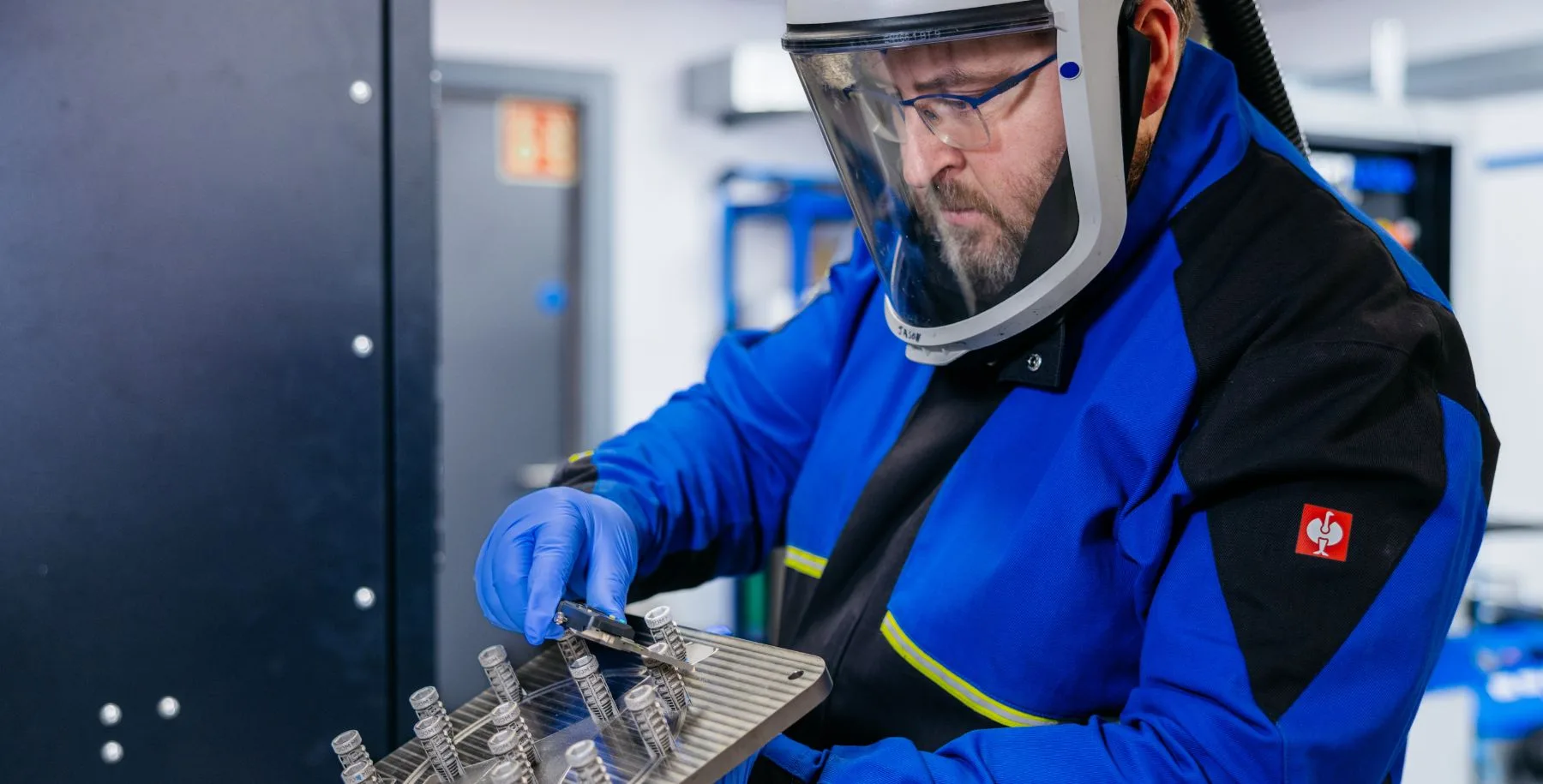
Additive Manufacturing Engineer inspects a series of SI Fixation Screws after printing.
4. Supporting the FDA 510(k) submission process
Croom Medical provided support to the customer throughout the 510(k) submission process, providing the necessary data for regulatory approval. This included material testing and manufacturing validation. Working closely with the customer, Croom Medical also supported in addressing multiple rounds of FDA queries, providing additional information, and conducting supplementary testing as needed.
5. Validation support enabling high variety, low batch orders
Croom Medical streamlined validation for the printing of mixed screw configurations on a single build plate. This enabled the customer to order diverse screw configurations based on market demand, reducing their inventory overhead.
We launched the product successfully in the market. Croom Medical accomplished something that four other vendors couldn’t.
Full FDA approval and market entry
Following full FDA approval, the SI Fixation Screw successfully entered the market. Production files were finalised, and Croom Medical transitioned from R&D to full-scale production. With a four-year collaboration, the customer now involves Croom Medical earlier in the product development phase, recognising their expertise and reliability.
About Croom Medical
Croom Medical is a leading contract manufacturer with 40 yrs experience delivering top-quality orthopedic implants. Leveraging their deep expertise and state-of-the-art manufacturing technologies, Croom Medical enables medical device OEMs to increase their production capacity and improve product quality, while reducing manufacturing costs. Their FDA-registered & ISO 13485 certified facility in Ireland, is supported by a dedicated team of 170+ professionals, including an award-winning RD&I team.
Discover more about Croom Medical’s Additive Manufacturing expertise.