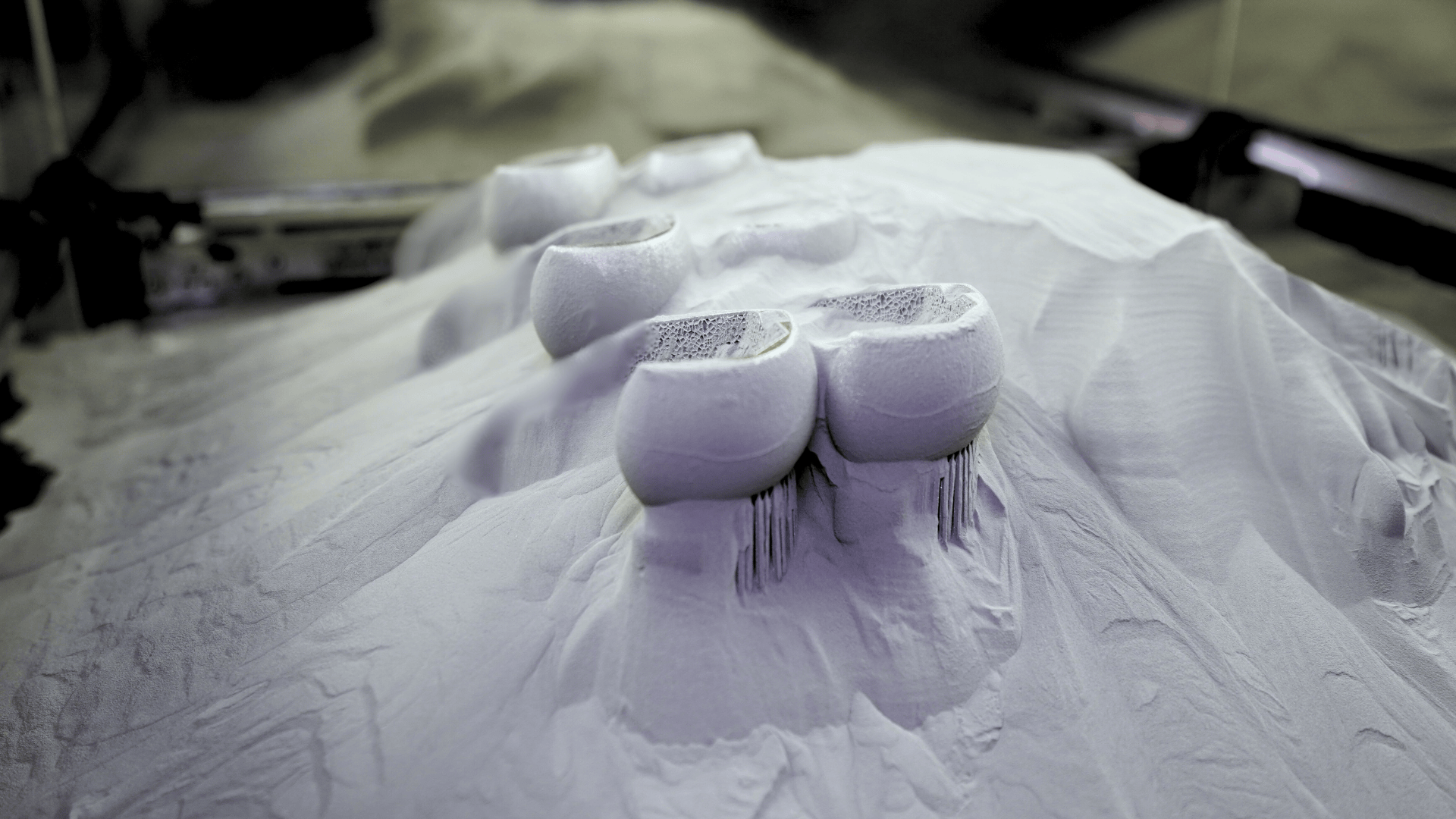
Additive manufacturing (AM) is reshaping the landscape of orthopedic implant design, enabling the manufacture of complex geometries and reducing time-to-market. In the case of Laser Powder Bed Fusion (L-PBF), osteointegration is a key factor driving its use, particularly for producing low-volume, high-variety medical implants with precise, patient-specific geometries.
Successful AM requires specific implant design approaches that differ from traditional manufacturing. In this blog post we will highlight the essential implant design elements your product development team need to consider to achieve optimal results in metal additive manufacturing.
1. Optimise Implant Orientation
The orientation of an implant during the 3D-printing process is crucial for quality and efficiency. It’s worth noting that components manufactured using additive manufacturing are anisotropic. This means that their strength can vary depending on their orientation relative to the build direction – an important consideration especially in load carrying implants.
Here’s what you need to keep in mind when designing your medical device:
Consider Feature Orientation: Holes, pockets and screw threads can be printed, however, it they are best printed typically in the Z-direction for better quality, reducing the need for support structures.
Downfacing Surfaces: Surfaces below a certain angle—typically 40° to 55°—may suffer from lower quality and rougher finishes. Designing your implant with minimal downfacing areas can enhance the quality of the final component.
Thermal Stress Management: During the 3D-printing process it is best to orient components to avoid large cross-sections, reducing thermal stresses and the risk of warping.
2. Minimise Support Structures
Support structures are often necessary but can increase costs and post-processing time. Strategies to minimise their use include:
Avoid Large Overhangs: Large overhang areas require significant support structures. Designing your implant with fewer overhangs or reorienting them during the printing process can reduce this need.
Precision Design: Use gradual transitions, such as fillets and chamfers – one of the most effective way to reduce supports. This will also help to reduce stress concentrations and improve as-printed accuracy.
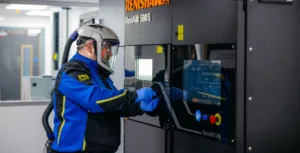
Additive Manufacturing Engineer operating Renishaw’s RenAM 500S machine, well-suited for printing high-precision orthopedic implants.
3. Material-Specific Design
Each material used in AM has unique properties and characteristics that influence the printing possibilities:
Titanium Alloys: These can achieve self-supporting angles as low as 30°, offering more design flexibility.
Steel, Aluminum, and Cobalt-Chrome: Generally, these materials require support angles between 50° and 55°. Align designs with these specifications for optimal results.
At Croom Medical we have great success 3D-printing titanium implants on our fleet of Renishaw, MLab and 3D Systems machines. By fine-tuning the process parameters and leveraging the design principles in this article, we’ve been able to achieve dimensional accuracy of ± 50 microns and superior mechanical properties for our customers.
4. Consider Small Features and Wall Thickness
The capabilities of AM machines, the material, orientation, and part geometry dictate the minimum feature sizes that can be effectively printed. Typically for Laser Powder Bed Fusion (L-PBF) the following guidelines apply:
Wall Thickness: Maintain a minimum of 0.20mm for gas-tight walls, adjusting thickness based on wall height to prevent deformation.
Pillar Diameter: Ensure free-standing pillars have a minimum diameter of 0.50mm to withstand post-processing.
5. Leverage Topological Optimisation
Additive Manufacturing enables the creation of lightweight, optimised structures that traditional manufacturing cannot achieve:
Weight Reduction: Implement lattice structures and topological optimisation to reduce weight while maintaining strength, ideal for medical device applications.
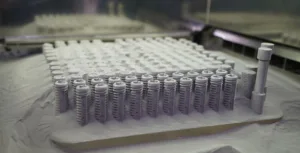
A batch of demonstration SI Joint Fixation Screws printed at Croom Medical’s Additive Technology Lab.
6. Facilitate Powder Removal
In metal Additive Manufacturing, unsintered powder can become trapped in internal cavities of the implant. To prevent this, consider these tips:
Incorporate Powder Removal Holes: Ensure internal cavities have access points for efficient powder removal.
Design for De-powdering: Avoid enclosed spaces where powder could be trapped, making de-powdering challenging.
7. Part Nesting
When designing your implant for AM, consider the potential for part nesting to maximise the number of implants produced in a single print run, decreasing production costs. To enable effective part nesting, your implant design must accommodate the use of support structures on both the top and bottom surfaces of the implant.
Conclusion
Designing for additive manufacturing (DfAM) demands a comprehensive approach that considers material properties, part orientation, support needs, and post-processing. By considering these design principles, you can harness the full potential of AM, reduce costs, and achieve high-quality results.
Discover how Croom Medical’s award-winning R&D team helped a leading spine OEM overcome the challenges of 3D-printing an innovative SI Joint Fixation Screw with fine, intricate features in our latest case study. Read more here.
Searching for expert guidance on your next additive manufacturing project?
Reach out to Croom Medical’s R&D team for specialised support in Design for Additive Manufacturing. Schedule a free 30-minute DfAM consultation today – contact us.
About Croom Medical
Croom Medical is a leading contract manufacturer with 40 yrs experience delivering top-quality orthopedic implants. Leveraging their deep expertise and state-of-the-art manufacturing technologies, Croom Medical enables medical device OEMs to increase their production capacity and improve product quality, while reducing manufacturing costs. Their FDA-registered & ISO 13485 certified facility in Ireland, is supported by a dedicated team of 170+ professionals, including an award-winning RD&I team.
Discover more about Croom Medical’s Additive Manufacturing expertise.